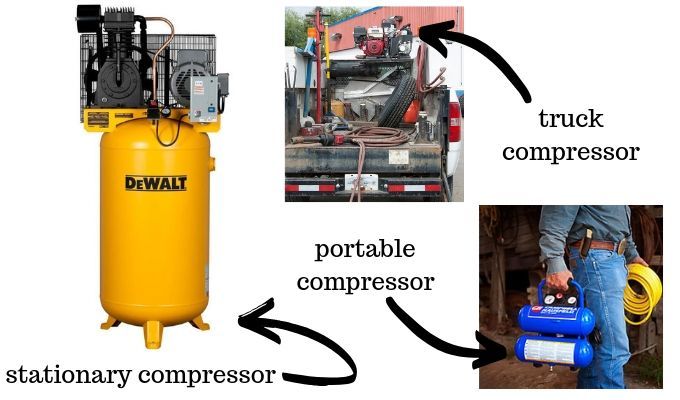
Air compressors are such a crucial piece of equipment in a wide array of different industries, which helps explain why there are dozens of different types of air compressors available on the market today.
Each type has its own advantages and disadvantages, which makes a certain type of air compressor more suitable for different tasks and workloads compared to others. Air compressor manufacturers have come up with dozens of different ways to compress air into a given space that you may be surprised at how many different operating principles there are to choose from.
In general, there are two broad classifications of air compressors. There are the ones that work by positive displacement, and others that work by roto-dynamic principles. In this article, we’ll go into more detail on positive displacement air compressors.
These are the ones that you will usually find in consumer grade equipment – their versatility and simplicity make the positive displacement air compressor the practical choice when it comes to portable and standalone compressed air applications.
Of course, no written guide on air compressors will be complete without at least touching on the more popular roto-dynamic compressor types. We’ll also take a look at the other aspects of air compressors, such as the number of stages, as well as some of the form factors available for portable air compressors.
Reciprocating (Piston) Air Compressor
Reciprocating air compressors are some of the most commonly used around the garage or the workshop for a wide variety of compressed air applications. This type of air compressor is based around a very simple design, with little in the way of dynamic adjustments.
The reciprocating air compressor is well represented in a wide range of pressure ranges, and they are practical and hold up well under work load.
Reciprocating compressors often use a spring-loaded piston as a way to drive air into a pressure chamber. Most models will have more than one piston connected by a crankshaft, which helps the unit make the most out of the power sent to them from the engine. In most air compressors, the crank shaft is either directly connected to an electric motor, gas motor or a diesel engine.
The principles of operation behind these kinds of air compressors are very simple. If you are familiar with how a manual bicycle pump works, then you already have a good grasp on how the reciprocating air compressor functions.
They can displace and compress air to one direction with the use of inlet and outlet valves arranged so that air can only move towards one side of the compression chambers.
Reciprocating air compressors are further classified as either single acting or double acting. Single acting compressors can actively push air towards one side of the piston – if you can imagine how a bicycle pump works, the plunger only offers resistance as you push down on it. The other end of the plunger is open to the air, and you don’t do any compression work when you are pulling it upwards.
Double acting compressors, on the other hand, have both sides of the piston sealed and equipped with intake and delivery valves. This type of air compressor can compress air during both the downward and upward stroke, due to the way the extra valves are set up along both ends of the piston chamber.
This arrangement not only ensures that both the forward and reverse motion of the piston contributes to air compression, but it also makes sure that the air output is more even since the compressor can actively put out air twice during one stroke cycle.
Reciprocating air compressors are capable of high PSIs, plus they are some of the most affordable compressors you would find. They are also simple machines that are easy to maintain or service. They do tend to lag behind CFM compared to continuous flow compressors, and they are also louder in operation.
Rotary Screw Air Compressors
Another common type of displacement compressor is the rotary screw type, which uses two screws that are intermeshed with one another with tight tolerances. As the two screws turn inside the compressor casing, the flutes of the screw drive down the pockets of air it collects, until enough pressure is built up that the delivery valve gets opened.
Unlike reciprocating compressors that rely on a rapidly moving piston, the rotary screw compressor is a much quieter piece of equipment. Since there is no stroke cycle, the air output of the rotary screw compressor is continuous and more stable. On the other hand, screw type compressors perform at their best in dealing with tasks that have a low air pressure requirement.
Double rotor screw compressors trap and seal in air through pockets formed by the flutes of the screws. The spaces between are made to tight tolerance and sealed with oil, lubricating Teflon based coatings or even water. This lets the screws move the air towards the direction of the pressure chamber.
The main advantage of rotary screw air compressors is their reliability – they deliver continuous airflow and often have a longer lifespan than reciprocating compressors.
They are also relatively quiet while operating compared to reciprocating compressors and the noise that their pistons make. On the other hand, rotary screw air compressors are more expensive up front, and then there’s the need for extensive skilled maintenance to get the most out of them.
Rotary Centrifugal Air Compressor
Rotary centrifugal air compressors used a rotating impeller to draw in and push air into a pressure chamber. These components are very similar to what you would see in an automotive turbocharger, and they are also used in industrial scale applications like those in oil platforms and fueling installations.
While centrifugal air compressors used impellers, the air flow is not directed to a central axis like you would find in any other systems that use a fan-like component.
Instead, the impellers of a rotary centrifugal air compressor force the air towards the outside perimeter of the compression chamber, and the blades add speed to the air before it is channeled out to the diffuser from one edge. The diffuser narrows down on its way to the pressure chamber or the next stage of the rotary centrifugal air compressor, which further increases the air pressure.
Rotary centrifugal air compressors often compress air in two or even three stages, which can make them more energy efficient than many displacement compressors and rotary screw types. They are also ideal for applications that require a stable supply of compressed air for sustained workloads.
Portable Air Compressors
There are a wide variety of portable air compressors today that lets you use your personal air tools even outside the workshop or the garage. Many of these portable compressors come in both gas powered and electric versions, and there is a multitude of choices when it comes to size, form factor, capacity, and weight.
Many of these portable air compressors are suited for inflating tires and running one or two basic air tools – the common limitation for these compressors is the capacity of their tanks.
Portable air compressors start from the personal pancake and hotdog models that you can put in the trunk of your car. Twin stack and upright tank portable air compressors are also available that offer higher capacities and pressure.
Stationary Air Compressors
Stationary air compressors cover the tasks that smaller portable air compressors may struggle with. Some of these stationary compressors do offer features that make the semi-portable, like lifting handles and wheels, but for the most part, you will set them up in one corner of the garage or workshop and they will be staying there for a while.
Some of these units can weigh a good 80 pounds or even more, and they have the tank capacity with the matching engine to deal with a wide variety of professional power tools.
In general, you will need a stationary air compressor to run tools that require a decent amount of CFM to operate, such as paint sprayers and sand blasters. You will also need them for a variety of applications that require a good amount of air pressure, such as for roof and flooring installations.
If you have a garage workshop, then you will need a good stationary compressor to run your pneumatic wrenches, and even more so once you get into operating pneumatic car lifts and jacks.
Most stationary air compressors start from the oversized upright tank or twin stack entry-level models to heavy-duty cabinet compressors that have to be professionally installed in the premises.
Truck Air Compressors
Professionals may have specific CFM and PSI requirements that off-the-shelf portable air compressors are simply not capable of. That’s why many contractors turn to mobile truck air compressors to deliver air on demand, with enough capacity to run even their most demanding pneumatic tools.
There are several approaches to getting a truck air compressor for your vehicle. The simplest is to get a tow-behind air compressor for your truck, which is ideal if you will be leaving the compressor on the job site for weeks at a time. Another solution is to mount a whole air compressor, engine and all, to the back of a truck or inside its cargo hold.
Some companies also offer kits and outfitting services that let operators install air compressor components into the engine bay of a compatible vehicle, which frees up the cargo hold or the back of the truck for other purposes. Many of these solutions are custom-made for specific truck models, and you may need to check if your vehicle warranties are still in effect after these modifications.
Single Stage (Electric) Air Compressors
Air compressors units can only achieve so much compression for a given volume of air that passes through the compression chamber. A single stage air compressor can achieve pressures of up to around 145 psi or a bit more, which is sufficient for a wide variety of applications.
Single stage electric air compressors are often found in portable models, where weight savings, energy efficiency, and portability are the main concerns.
Note that many single stage air compressors may come with two cylinders – this does not mean that the compressor is a two stage model. More cylinders simply increase the storage capacity of the air compressor in this case.
Two Stage (Electric) Air Compressors
A single stage electric air compressor may struggle to achieve pressures past 145 PSI, without the whole setup becoming too bulky. To achieve higher pressures, air compressor makers turn to multi-stage setups that take the compressed air from the first stage and compress it even further.
Most electric air compressors are capable of compressing air at the second stage to around 180 PSI, before this double-compressed air is cooled and sent to the pressure tank.
Different Air Compressor Styles
Air compressors come in a wide variety of shapes and styles to fit just about any need for pressurized air. From the smallest pancake type compressors to industrial cabinet installations, there’s an ideal size available for your specific needs.
Pancake compressors are some of the smallest kits you can find, and they typically come with squat, round six-gallon tanks with the pump on top. These can operate a brad nailer or fill up tires, and other lightweight tasks.
Hot dog compressors and twin stack air compressors are a step up from the pancake style. These models come with one or two elongated tanks, and enough pressure and capacity to run nail guns, sanders, and air brushes.
Moving up from the hotdog models, you will find wheelbarrow compressors that look similar to portable electric generators. They come with handles and at least one wheel, and they have enough power and capacity to run multiple heavy duty tools such as pneumatic wrenches and sand blasting cabinets.
If you need more capacity, then it is time to consider stationary air compressors. The simplest ones have an oversized tank cylinder with the right pump to match, and this will be plenty for many of your heaviest pneumatic tools.
For industrial scale workshop floors, there are the cabinet air compressors that come equipped with filtered intakes, vents, and service panels for the utmost in reliability.